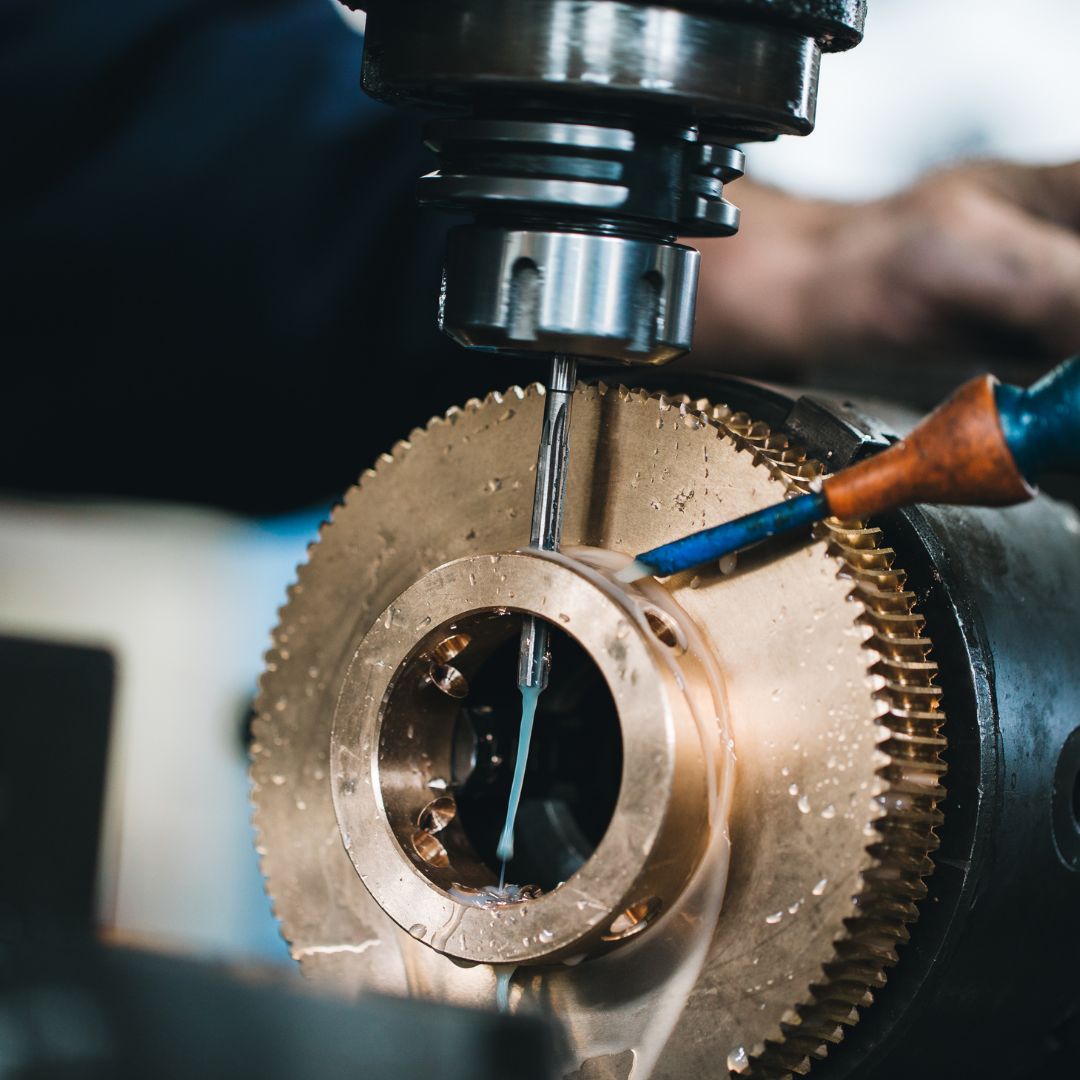
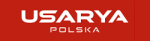
Implementation for Usarya Polska
Our client is an innovative Polish company, specializing in the production of advanced stone collection machines. It was created thanks to the ingenuity and joint commitment of three enthusiasts and outstanding constructors. For its breakthrough solutions, thanks to which such hard work has been mechanized, the company has received numerous national and foreign awards. The high quality of the offered machines goes hand in hand with care for modern management and monitoring of production.
Project scope
Due to the growing demand for precise monitoring of work processes and optimization of working time, the company faced the challenge of improving work organization. The company's management was looking for a solution that would allow for better management of human resources, elimination of inefficiencies and increased control over production. The project involved 25 employees employed in various production positions.
WHAT WE DID?
We have implemented a comprehensive system of Time Recording (T&A) and Activity Records, which enabled:
- automatic recording of employees' arrival and departure times,
- monitoring of employee breaks in order to analyse the effective use of time,
- detailed tracking of activities performed by employees at different stages of production.
Thanks to the use of our system, the company has gained access to precise data on working time and individual operations carried out by employees. This information has become crucial for improving the management of production processes.
WHAT EFFECTS DID IT BRING?
1. Increase in employee self-control
The introduction of the T&A system has significantly improved the punctuality of the team. Employees managed their breaks more consciously, which translated into their efficiency and work organization.
2. Improve performance
Detailed data on the activities performed allowed for the identification of bottlenecks in the production processes. This allowed management to make informed decisions about reorganizing work and eliminating time waste.
3. Better quality control and problem identification
The activity recording system made it possible to determine exactly which employee was responsible for which stage of production. In the event of a complaint, it was easy to identify the potential source of the problem and take corrective action, including additional training for employees.
4. Increase production capacity without the need to hire new employees
By analyzing uptime and eliminating inefficient processes, the company was able to increase its efficiency without additional personnel costs. Planning optimization allowed for better use of available human resources. Easier planning and settlement of working time
5. Automation of the time and attendance process
The full settlement of working time, electronic registration, and an online list of employees have minimized errors in records and simplified HR administration. Accurate data has enabled fairer and more transparent accounting of performance-related salaries and bonuses.
Additional benefits of the implementation - information about the necessary training of employees
The activity recording system made it possible to determine exactly which employee was responsible for which stage of production.
In the event of a complaint, the Time Harmony system allowed for quick and precise finding of information about who made a specific part of the machine. This made the complaint process more transparent and efficient, and the company was able to implement corrective actions immediately.
Employees who made defective elements were sent to specialized technical training tailored to their scope of work. These trainings included both theoretical issues related to correct assembly techniques and practical workshops to improve skills. In addition, the most common errors were analysed and preventive procedures were developed to avoid similar problems in the future.
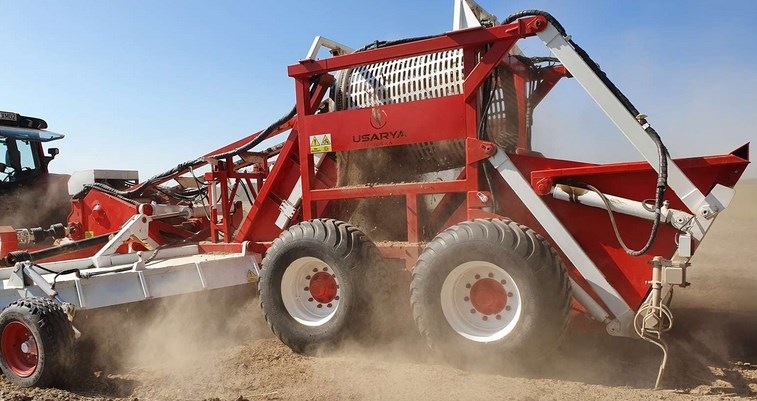
Cooperation
Our cooperation with Usarya Polska began in March 2023 and has been successfully continued to this day, which proves mutual trust and the effectiveness of the implemented solutions.
Thanks to the implementation of T&A modules and the Activity Records of our system, USARYA POLSKA SP. Z O.O. has significantly improved its production processes. The company not only increased control over the team's working time and efficiency, but also improved production quality and operational efficiency. The implementation of technology has avoided the need to increase employment and at the same time raised the standards of work management.
The system proved to be a key tool in the process of optimizing production and personnel management, contributing to the further development of the company and strengthening its position on the market.
"Generate savings. Increase production efficiency."
Time Harmony has streamlined a number of time planning and accounting processes, leading to significant savings and increased production efficiency. In addition, the system provided valuable information useful in the complaint process. It is a well-thought-out, intuitive and easy-to-use system.
Milena Wiśniewska
Management Board Member, Usarya Polska Sp. z o.o.