Time Harmony optimizes processes in companies from various industries
Our advanced system is used by companies from various industries and sectors to optimize processes, increase efficiency, improve coordination, planning and time management.
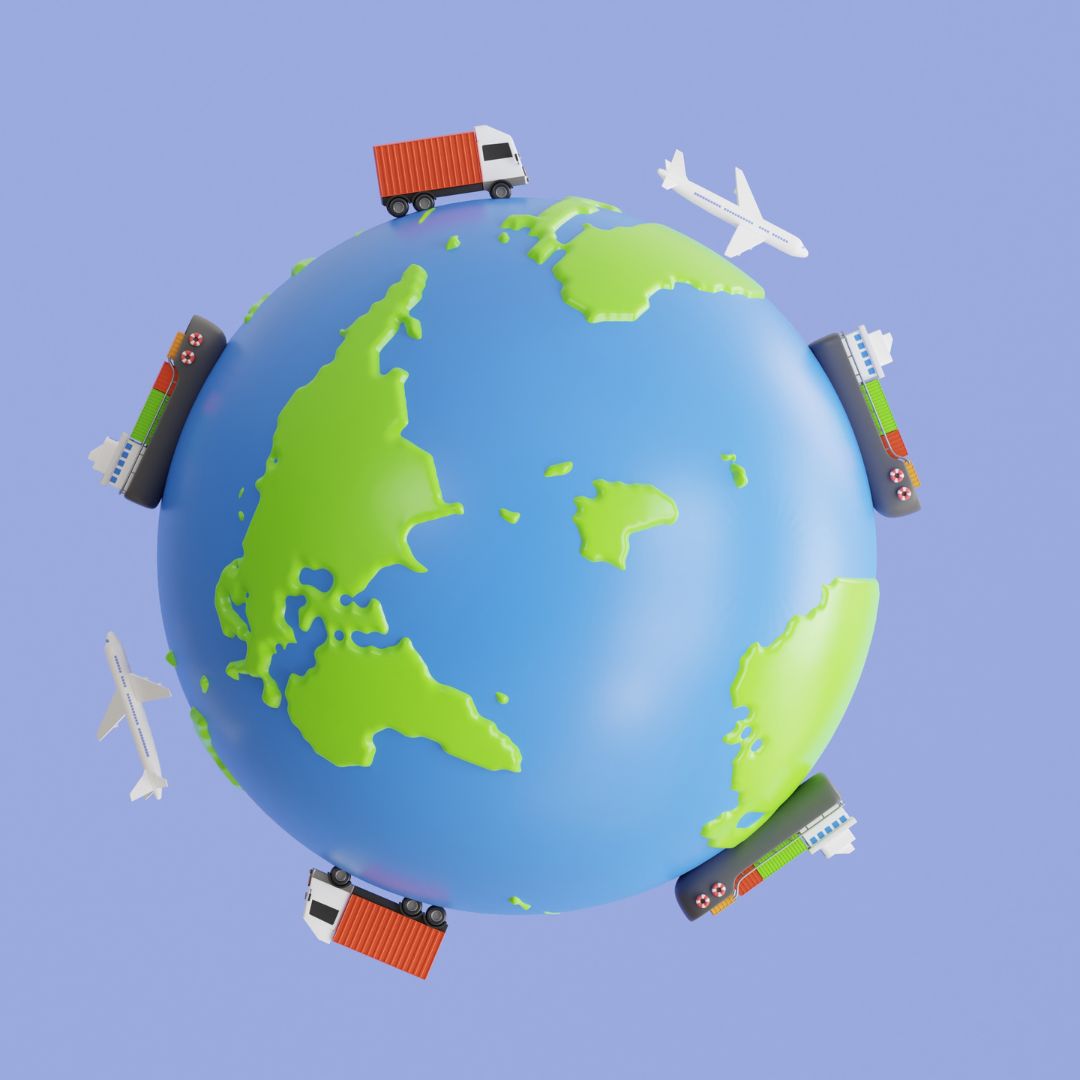
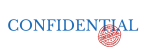
Labour Management Project in an international logistics company
We are the main supplier of a work management system (LMS) as part of an international Labour Management project for a global logistics operator.
For the purposes of this project, we have expanded Time Harmony with functionalities tailored to the needs of global companies. We have introduced support for multiple time zones, local holiday calendars and absenteeism limits. In addition, the system has been extended to support any language, which increases its versatility and facilitates implementation in international structures. Time Harmony is a comprehensive tool that offers unified reporting and cross-sectional visibility into work processes, supporting effective management on a global scale.
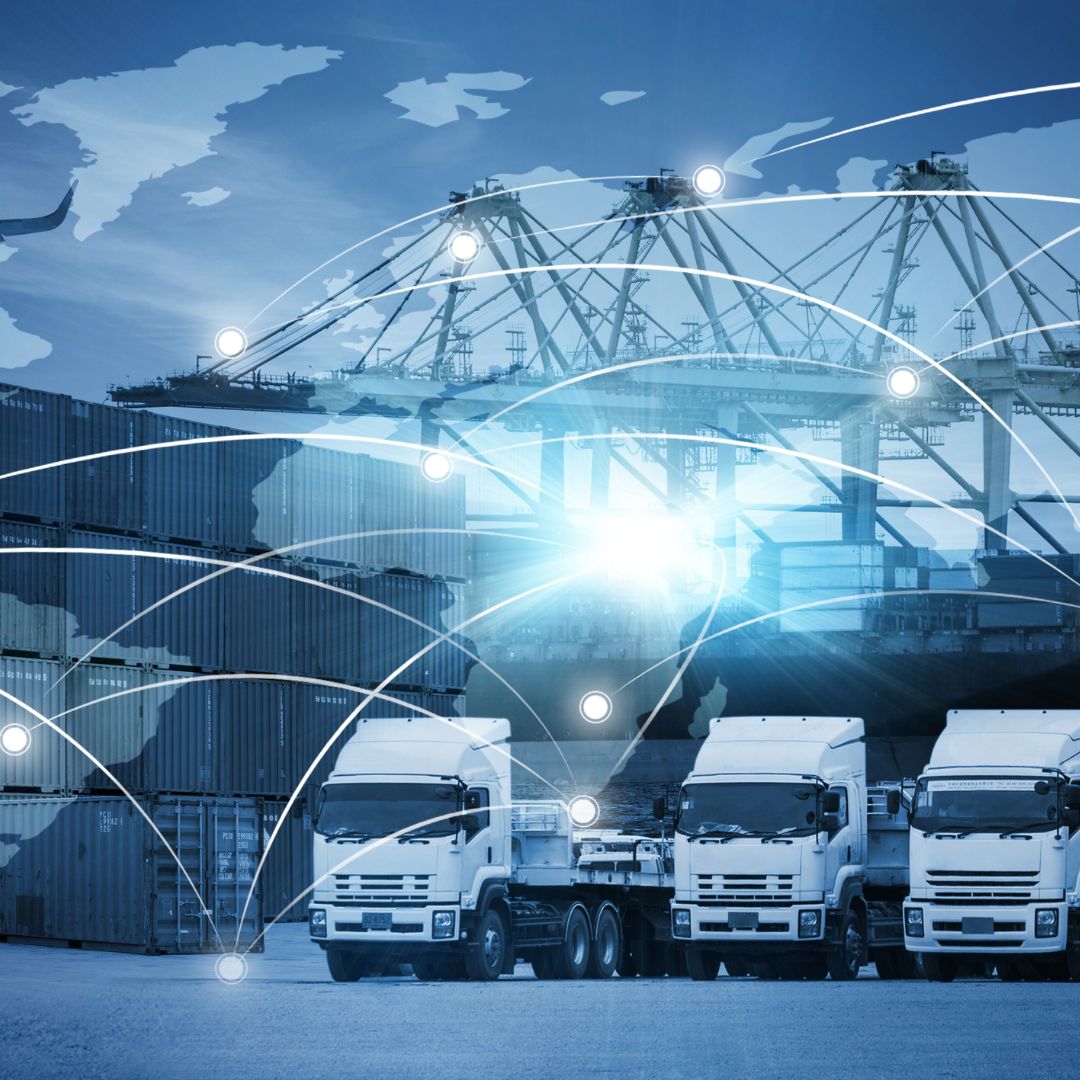
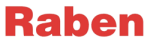
Measuring warehouse processes and measuring the profitability of VAS orders
The project was aimed at indicating the efficiency of processes vs. assumptions and calculating the profitability of individual orders on the basis of labor costs estimated on the basis of the activities performed.
The Time Harmony system provided data to calculate the profitability of VAS orders, as well as contributed to the improvement of work organization and planning.
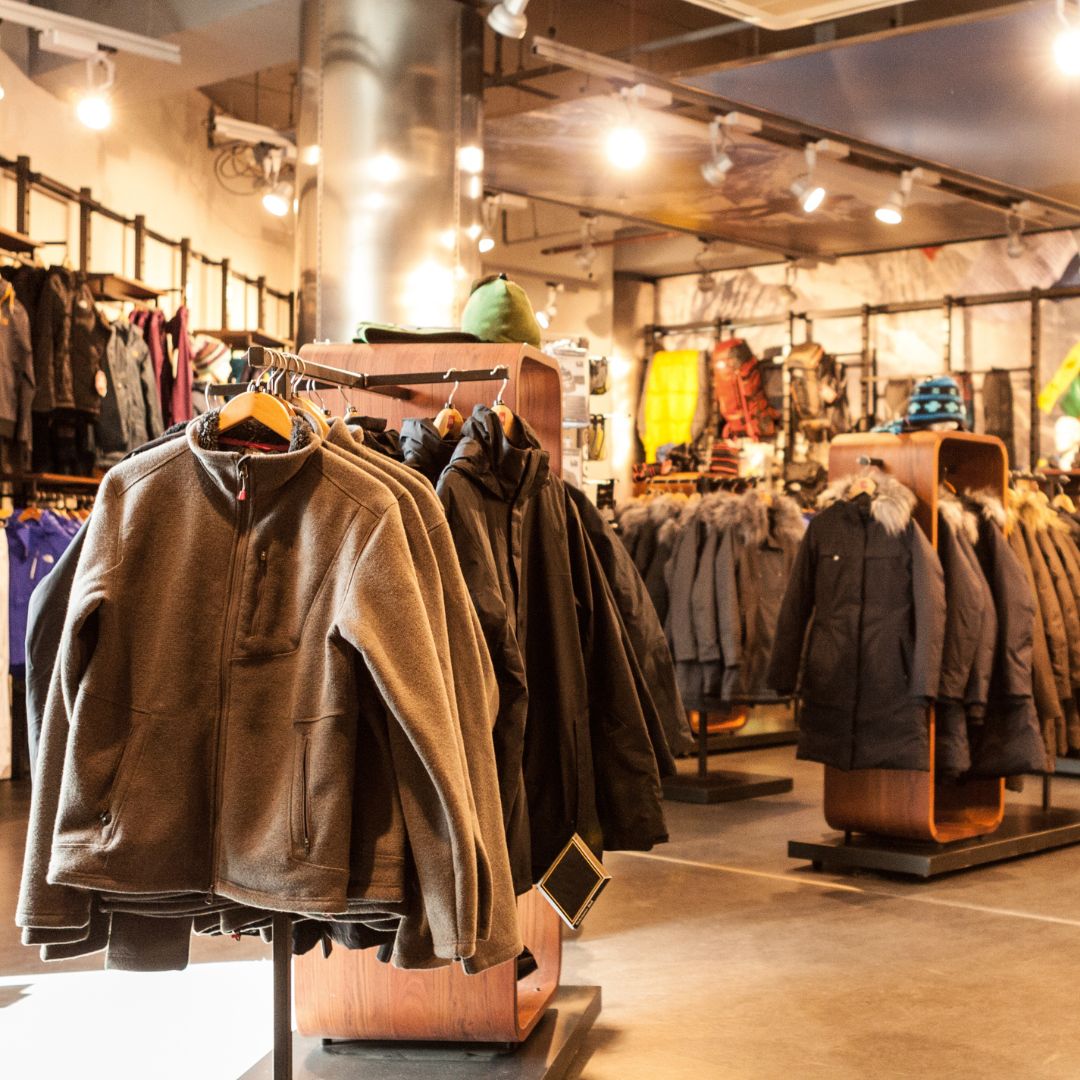
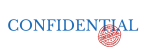
Savings from the reduction of unproductive activities
One of our clients, who owns a network of logistics and warehouse centers, declared a decrease in unproductive activities from over 20% in the first month of Time Harmony implementation to about 2% after a few months of working with the system.
In the case of logistics operators, employing thousands of employees, such a level of reduction in non-system activities means savings of many millions of zlotys per year.
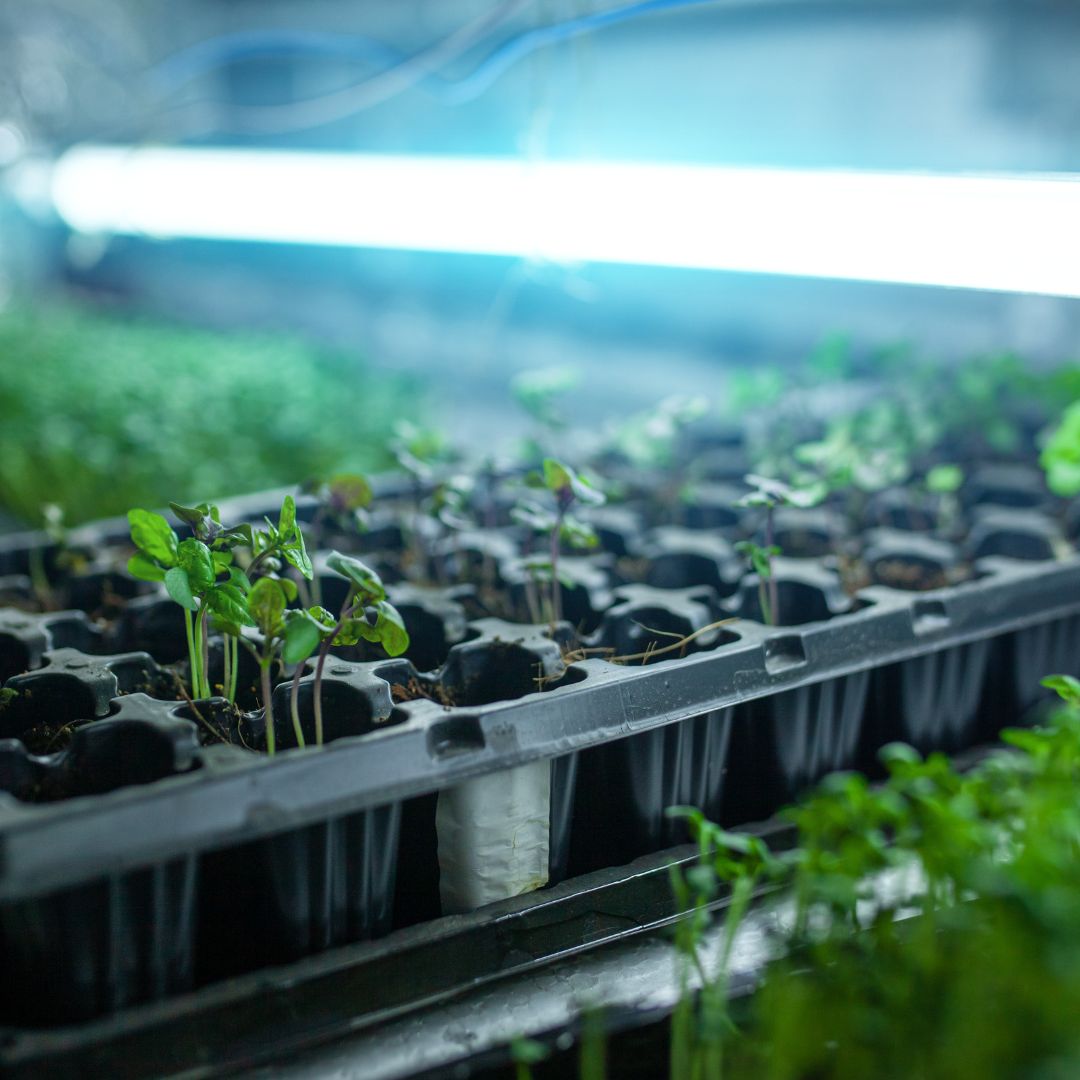
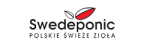
Collection of information on the number of units of an item produced. Identification of defective entities.
An example of implementation in a company outside the logistics and warehouse industry.
The main assumptions of the project: management of the production process, measurement of the pace of work, identification of defective goods. In addition, for the purposes of the project, the system was integrated with access control devices to guarantee hand disinfection before starting work.
Our clients are dynamic, modern companies that base the process of managing the work of teams on a set of reliable, credible online data.
Rhenus Delivery Services
#warehousingGrupa Progres
#employment agenciesFast Service Group
#employment agenciesRaben Polska
#warehousingDr. Max Lekomat
#warehousingAara Printing House
#productionConfidential_Perfumery
#warehousingConfidential_logistics operator
#warehousingBookkeeping Office
#serviceBiuro Innowacje
#serviceViapharma
#service, #warehousingOtrębusy Bakery & Confectionery
#serviceUsarya Polska
#productionSwedeponic Polska
#productionLogistics company
#warehousingWe work on the development of the system every day
+
Countries where we have implemented Time Harmony
k +
Employees covered by the system
+
Devices connected to the system